Discover why some of the world’s leading industrial companies choose the Honeywell range of aluminum brazing fluxes. In addition to standard formulations we have the expertise to adapt brazing fluxes to fit the individual environments and equipment of our customers.
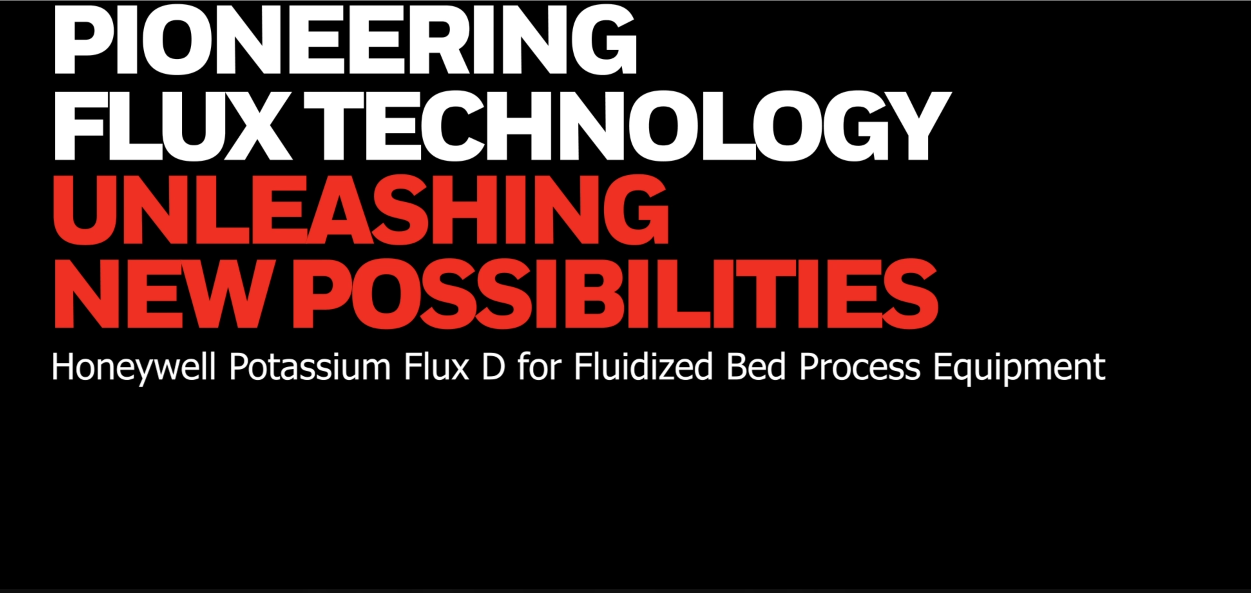
Our Aluminum brazing flux paste, paint, powder, and blends portfolio is constantly expanding to complement our existing range of high quality, consistent and reliable fluxes – serving customers in a wide range of industries including:
- Automotive
- Heating, Ventilation, Air conditioning cooling (HVAC)
- Industrial equipment
- Heavy duty vehicles
- Aerospace
- Brazing consumables
- White goods
Take a moment to view our Aluminum brazing flux paste, paint, powder, and blends portfolio.
FLUXING AGENTS | ||||||||||
KAIFx | CsAIFx | ZnF2 | LiF | KF | NaF | Li3AIF6 | Na3AIF6 | K3AIF6 | K2TiF6 | |
Standard aluminum-brazing flux | X | |||||||||
Aluminum-brazing flux for high magnesium containing alloys | X | X | ||||||||
Low-melting-point flux for flame brazing | X | X | X | |||||||
Non-inhalable dust grades | X | X |
FLUX FORMULATIONS | ||||||||||
KAIFx | CsAIFx | ZnF2 | LIF | KF | NaF | LI3AIF6 | Na3AIF6 | K3AIF6 | K2TIF6 | |
Powder blends | X | X | ||||||||
Flux suspension | X | X | ||||||||
Paint flux | X | X | ||||||||
Flux paste | X | X | ||||||||
Brazing paste | X | X |
FLUX ADDITIVES | ||||||||||
KAIFx | CsAIFx | ZnF2 | LIF | KF | NaF | LI3AIF6 | Na3AIF6 | K3AIF6 | K2TIF6 | |
Aluminum alloys containing magnesium | X | X | ||||||||
Optimize melting behaviour | X | X | X | |||||||
Reduce residues solubility | X | X | ||||||||
Improve oxide solubility | X | |||||||||
Reinforced aluminum-matrix composites | X | |||||||||
Corrosive fluxes | X | X | X |
Potassium Fluoroaluminate flux (KAlF4) and Cesium Fluoroaluminate flux (CsAlF4) are also available in a range of grades to suit a wide number of applications.
ASSAY |
|||||||||
---|---|---|---|---|---|---|---|---|---|
Article Number | Type | F | Al | K | Fe | Ca | Melting point onset | Loss on ignition | Particle size (D50) |
01774 – UF | Ultrafine | 47- 53% | 14 -18% | 27 – 39% | ≤0,03% | ≤0,1% | ≤555°C | ≤5% | 5 – 10µm |
01740 – F | Fine | 47- 53% | 14 -18% | 27 – 39% | ≤0,03% | ≤0,1% | ≤555°C | ≤2,5% | 8 – 12µm |
01732 – M | Medium | 47- 53% | 14 -18% | 27 – 39% | ≤0,03% | ≤0,1% | ≤555°C | ≤2,5% | 10,5 – 15µm |
01776 – D | Dry | 47- 53% | 14 -18% | 27 – 39% | ≤0,03% | ≤0,1% | ≤555°C | ≥ 15µm |
ASSAY |
||||||||
---|---|---|---|---|---|---|---|---|
Article Number | Type | F | Al | Cs | Melting point onset | Loss on ignition | pH (10%, 20°C) | Particle size (D50) |
01773 – N | normal | 28- 33% | 8 -12% | 56 – 62% | ≤445°C | ≤3% | 4 – 11 | 5 – 20 |
01799 – S | special | 28- 33% | 8 -12% | 56 – 62% | ≤445°C | ≤3%* | 4 – 11 | 5 – 20 |
01781 – HW | high wetting | 28- 33% | 8 -12% | 56 – 62% | ≤445°C | ≤5% | 4 – 11 | ≥ 5µm |
*application test
Advantages Of Honeywell Brazing flux
Honeywell Potassium Fluoroaluminate flux (AL-2805) enables a more robust and efficient brazing process when compared to other fluxes, and is characterized by a uniform amorphous and less abrasive morphology, and a high reactivity with aluminum oxide.
A lower flux melting point of 552 (± 3.0°C)
Honeywell Potassium Fluoroaluminate flux (AL-2805) has a unique multi-constituent phase, with amorphous amounts, providing a melting point of 552 ± 3.0°C. This melting point is 25 °C lower than the eutectic melting point of an Al-Si filler metal.
Customer Benefits:
- Low melting point
- Reduced corrosion and abrasion
- Controlled and narrow particle size distribution
- Excellent free-flow and dispersion properties
Customer Benefits:
- Wider flux reactivity range
- Up to 20% extra time for improved cleaning and oxide removal
- Energy savings drive eco-balance and reduce cost
- Higher reactivity enables lower flux loading
- Robust brazing process
A more controlled and narrow particle size distribution
Honeywell Aluminum flux features controlled particle sizes to meet and exceed customer product and process requirements :
- Narrow particle size distribution
- High batch-to-batch consistency
- Fast and complete dispersion in solution and slow settling
- Leading to reduced corrosion and abrasion
Customer Benefits:
- Homogeneous distribution on parts and in paints / pastes
- Easy and fast dispense due to uniformity of particles
- No plugging of nozzles and pipes
- No material loss on filters
- No yield loss due to assembly defects
- Uniform surface coverage
- Robust application process
Ready To Connect?
For information about how we can help your business.